Mapeamento de Processos | Controle da qualidade em 100% dos setores da empresa
Mapeamento de Processos | Controle da qualidade em 100% dos setores da empresa
O projeto de Mapeamento de Processos tem como principal objetivo padronizar e organizar a forma como a empresa trabalha. Ou seja, tornar compreensível todas as etapas de um fluxo de trabalho.
Além disso, define os responsáveis por cada procedimento. Ao passo que, busca otimizações para eliminar atividades que não agregam valor ao produto ou serviço. Dessa forma é possível reduzir custos, tempo, perdas e retrabalhos.
O projeto em questão foi realizado em uma empresa de autopeças, especializada no desenvolvimento e fabricação de polias e tensionadores.
Nesse sentido, o portfólio da organização apresentava mais de 800 itens de diversas aplicações em veículos automotores. No entanto, a empresa enfrentava um grande desafio em relação ao controle da qualidade de seus produtos. O qual era inexistentes em 80% dos setores.
Portanto, nesse projeto de Mapeamento de Processos foram padronizados os métodos da produção e estabelecidas as responsabilidades dos setores.
Dessa forma, foi possível levantar indicadores de controle da qualidade com o intuito de monitorar e controlar a efetividade dos procedimentos.
Desenvolvimento do Projeto
O projeto se iniciou com a análise dos 800 tipos de peças fabricadas pela indústria. Sendo que cada peça possui diversos componentes e cada componente é fabricado em um setor produtivo distinto dentro da própria empresa. Portanto, para facilitar a visualização dos processos, dividimos o mapeamento em duas etapas.
A primeira etapa com foco nos processos produtivos realizados para a fabricação dos componentes. Já a segunda etapa, focalizando na montagem das peças.
Dessa forma, nós separamos os diversos tipos de componentes produzidos em cerca de 10 famílias. Logo depois, verificamos em quais setores fabris cada família de componente transitava.
Além disso, nós priorizamos os tipos de peças montadas na companhia para realização dos mapeamentos. Ao invés de mapearmos a montagem de 800 produtos, foi necessário mapear a montagem de 100 produtos.
Em seguida, identificamos que diversos tumultos que ocorriam na linha de produção eram devidos às falhas de comunicação e desvios de ordens.
Com isso, realizamos reuniões com os donos da empresa para verificar qual a responsabilidade de cada setor e como o mesmo deveria se impor em relação a isso. Como resultado, foi criado um manual de responsabilidades de cada setor.
Posteriormente, elaboramos mais dois manuais, os quais foram focados na produção. Um deles com a finalidade de explicar os processos produtivos realizados em cada setor para a fabricação dos componentes. Já o outro com o objetivo de explicar a montagem de cada uma das 100 peças mapeadas.
Outro ponto observado foi referente ao controle da qualidade das peças. Sendo que, apenas 20% dos setores possuíam folhas de verificação da qualidade, as quais não geravam indicadores.
Além disso, identificamos a falta de controle das perdas geradas nos setores. Assim, criamos planilhas que geram indicadores responsáveis pela verificação da qualidade dos componentes e das peças fabricadas pela organização.
Conclusão
Para a realização do projeto, utilizamos três ferramentas da qualidade:
- Gráfico de Pareto: para a priorização das peças;
- Folha de verificação: para coletar e analisar dados referentes a qualidade das peças;
- Estratificação: a qual foi incorporada às folhas de verificação distribuídas aos setores, com a finalidade de separar os dados.
O organograma institucional também foi utilizado pela equipe para definir os papéis de cada setor e também os graus de hierarquização.
Portanto, como resultado da consultoria, a empresa obteve um manual de responsabilidades de cada setor para evitar falhas de comunicação e desvio de ordens.
A empresa obteve também o processo produtivo dos componentes e o processo de montagem mapeados e padronizados. A partir disso, foram elaborados mais dois manuais com o intuito de diminuir erros dos operadores.
Além disso, a consultoria fez com que a verificação de erros, que antes ocorriam em apenas 20% dos setores, começasse a ocorrer em 100% deles.
Enfim, a empresa que antes não obtinha nenhum indicador de perda, passou a verificar a qualidade da fabricação de seus produtos.
Essa medida contribui para a ODS 16, item 16.7. – Garantir a tomada de decisão responsiva, inclusiva, participativa e representativa em todos os níveis.
Para saber mais sobre o nosso serviço de Mapeamento de Processos, entre em contato conosco! Baixe também nosso infográfico sobre como aplicar indicadores efetivos na sua empresa.
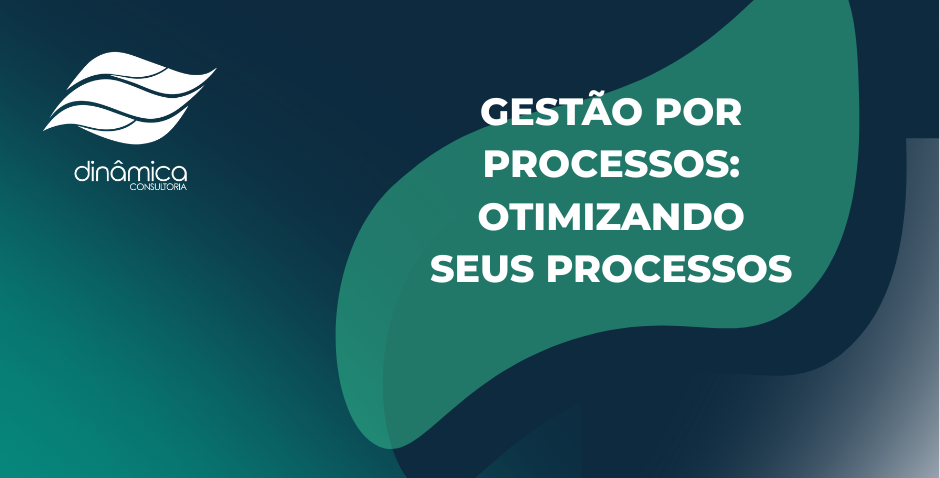
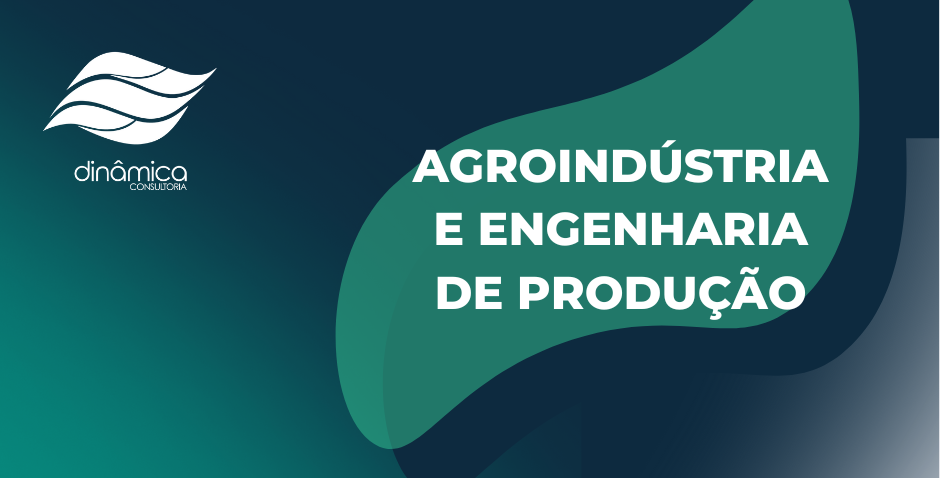
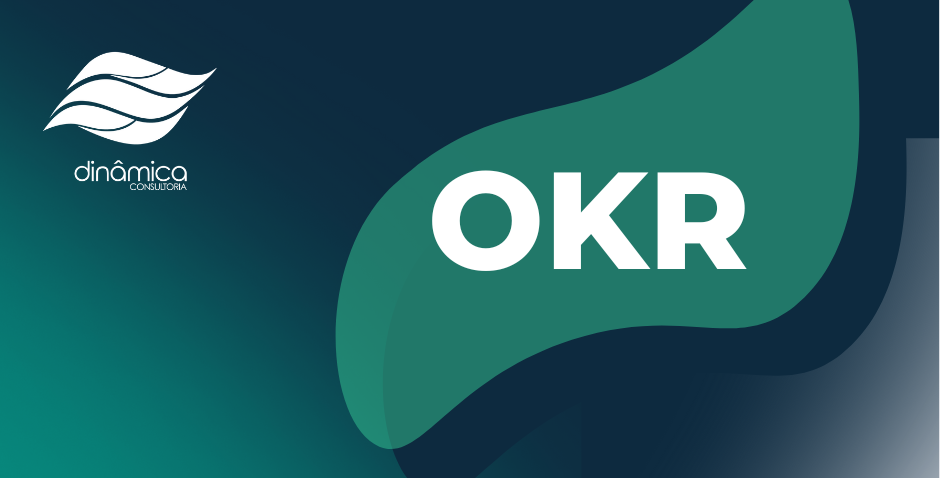
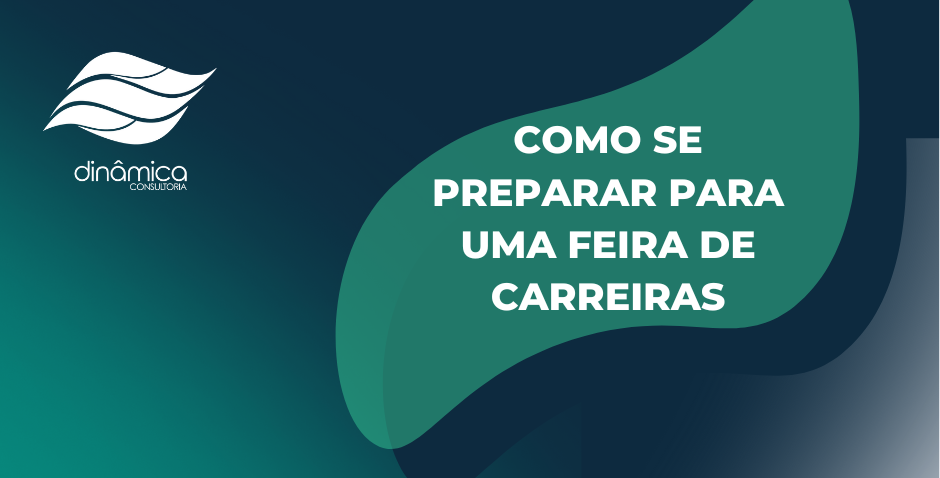
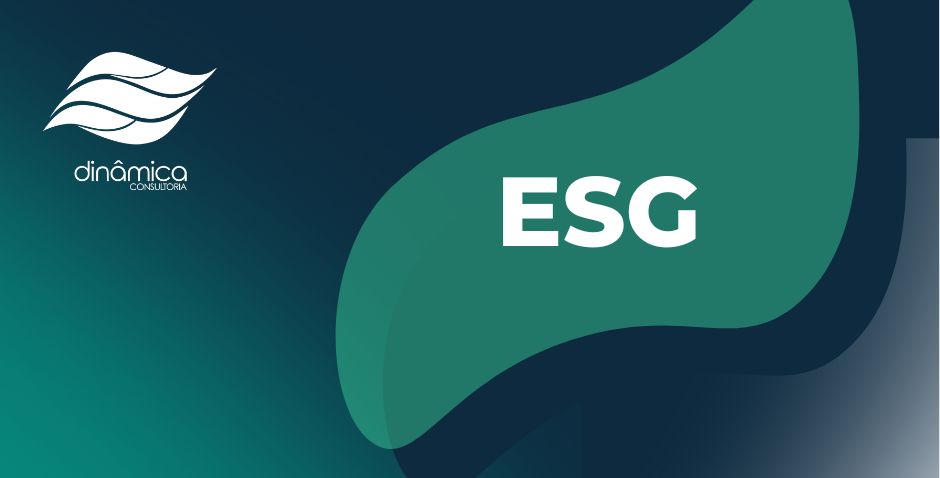
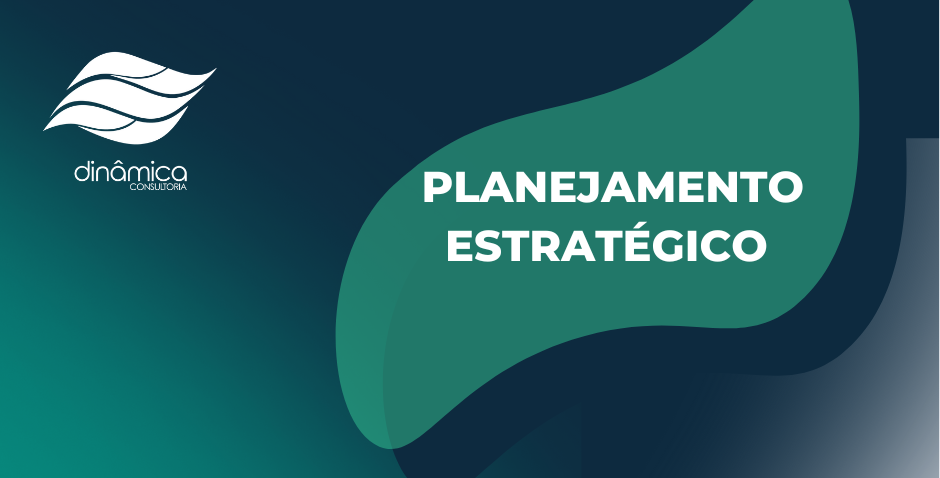
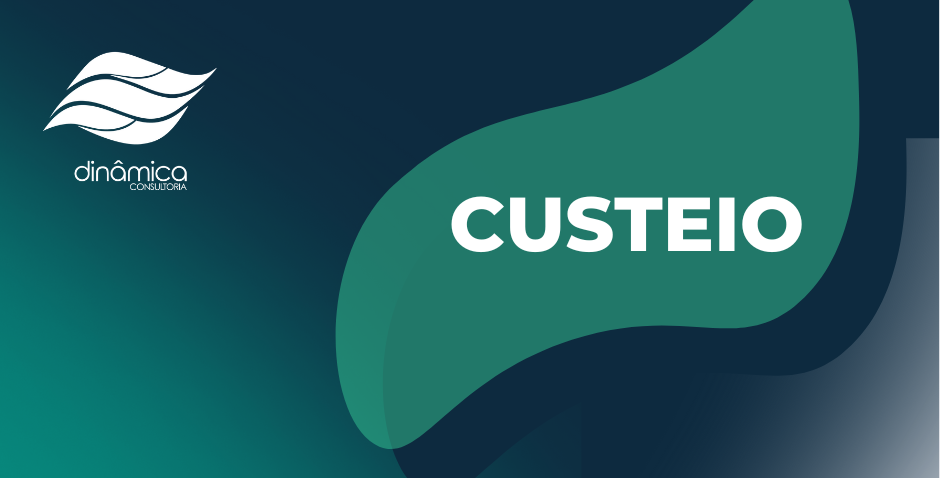