Ciclo PDCA e SMED | Redução de setup e aumento da eficiência no processo produtivo
Ciclo PDCA e SMED | Redução de setup e aumento da eficiência no processo produtivo
O projeto foi realizado numa empresa no ramo da indústria de produtos odontológicos que enfrentava problemas significativos com o lead time de produção e que afetavam diretamente a eficiência da produção como um todo. Dessa forma, os gestores da empresa buscaram a ajuda de uma consultoria especializada para identificar os principais gargalos e implementar melhorias no processo produtivo.
Para solucionar esse problema, a equipe da Dinâmica Consultoria trabalhou em conjunto com a equipe da empresa a fim de identificar soluções para reduzir o tempo de setup. Foram realizados estudos detalhados sobre o processo de produção e implementadas mudanças para melhorar a eficiência do processo, incluindo a padronização das etapas de setup e a eliminação de atividades desnecessárias.
Desenvolvimento
A primeira etapa do projeto consistiu em identificar os problemas existentes no negócio e definir as prioridades para cada solução. Ainda no período de entendimento dos fluxos e processos internos, foram feitos mapeamentos de todos os setores da empresa, incluindo os setores de Misturas, Embalagem, PCP e Laboratório.
Em seguida, a equipe iniciou o processo de identificação de problemas, estudando os setores mapeados e seus desperdícios, com o objetivo de entender quais necessitavam de melhorias urgentes. Logo após, foram realizadas pesquisas com os próprios funcionários para entender quais eram os maiores problemas e possíveis soluções, priorizando-os com a Matriz GUT.
Após a identificação dos gargalos em cada setor, os esforços foram concentrados no estudo das paradas de máquina, que foram apontadas como um problema crítico por vários funcionários. Durante essa etapa, o setup da máquina foi identificado como uma das principais causas de parada, o que permitiu à equipe focar-se em encontrar soluções para reduzir o tempo de setup e melhorar a eficiência do processo produtivo como um todo.
Na segunda etapa do projeto, o objetivo era desenvolver meios para tornar possível a aplicação de soluções para os problemas encontrados anteriormente. Para isso, a equipe se prontificou a estudar a principal máquina utilizada pela empresa e entender como eram programados os setups para ela.
Para solucionar a questão do tempo necessário para preparar a máquina, foi preciso compreender o fluxo de atividades envolvido na montagem, desmontagem e limpeza da máquina. Com isso em mente, o time filmou, mapeou e cronometrou todas as atividades que eram realizadas por um único colaborador.
E então, baseada nessas informações, a equipe foi capaz de montar uma tabela mapeada de todas as atividades exigidas pelo processo de setup e determinar o tempo necessário para cada uma delas. Essa tabela forneceu uma visão clara do processo de setup como um todo, permitindo que fossem identificadas oportunidades para melhorar a eficiência do processo e reduzir o tempo necessário para completar algumas tarefas em específico.
A partir dessas análises foi possível calcular o tempo gasto para cada parte do processo, resultando num tempo total de 4h49min para as atividades de setup e 7h24min incluindo horas ociosas dos operadores.
Além disso, a equipe conseguiu identificar quais elementos internos poderiam ser transformados em externos. Isso significa que atividades que antes só podiam ser realizadas quando a máquina estava parada poderiam ser realizadas enquanto a máquina estava em funcionamento, reduzindo ainda mais o tempo necessário para completar o setup.
Com os tempos e atividades em mãos, algumas melhorias foram apontadas para o processo, incluindo:
- Lavagem de todos os utensílios a serem utilizados antes de iniciar as atividades;
- Ter uma bancada com equipamentos extras próximos ao operador;
- Aumento no número de operadores para realizar o setup.
Entre outras melhorias significativas. Assim, com as otimizações implementadas e o setup realizado com dois operadores em atividade, foi possível chegar em 2 horas e 7 minutos de tempo de operação em setup, somente em atividades não ociosas, totalizando uma redução de 56,4% em relação aos tempos anteriores, e que também foi responsável por proporcionar uma redução de custos com produtos perdidos de R$63.316,39 para R$15.268,79, uma redução expressiva de 75,8%.
Para finalizar o projeto, todas as atividades realizadas nas etapas anteriores foram documentas na forma de um POP (Procedimento Operacional Padrão), para facilitar o entendimento dos processos caso algum operador novo entrasse na operação
Conclusão
Dessa forma, é evidente o contentamento da empresa com relação aos trabalhos executados pela Dinâmica Consultoria. Também é importante ressaltar que todas as entregas realizadas contribuíram para que o cliente entendesse a importância das melhorias e otimizações no seu processo produtivo e aproveitasse os resultados obtidos.
Caso tenha ficado alguma dúvida, entre em contato conosco e faça um diagnóstico gratuito!
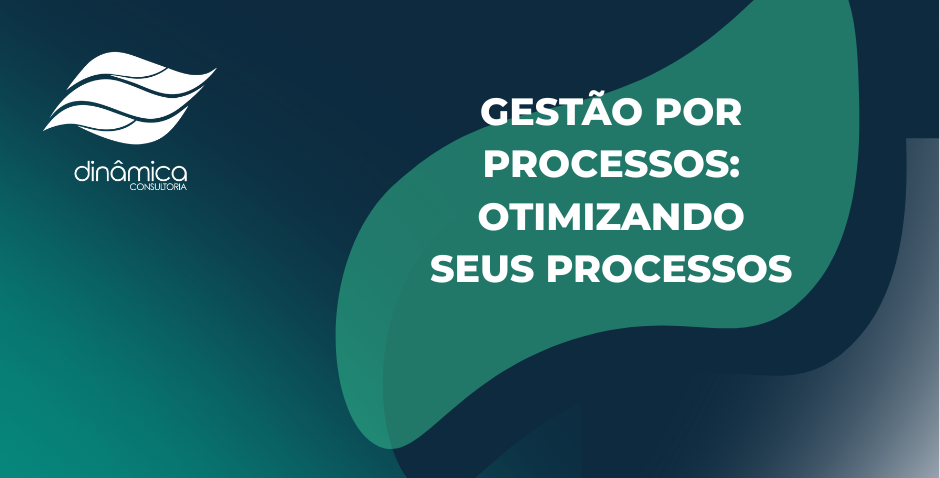
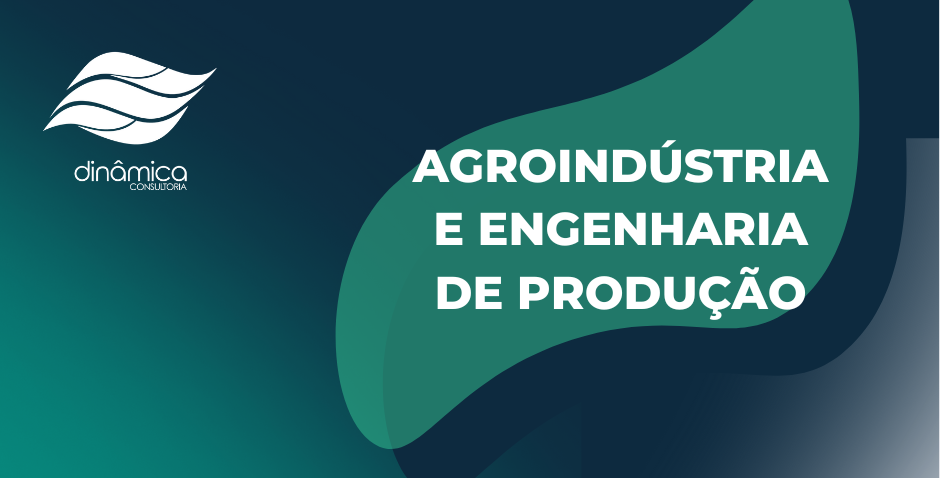
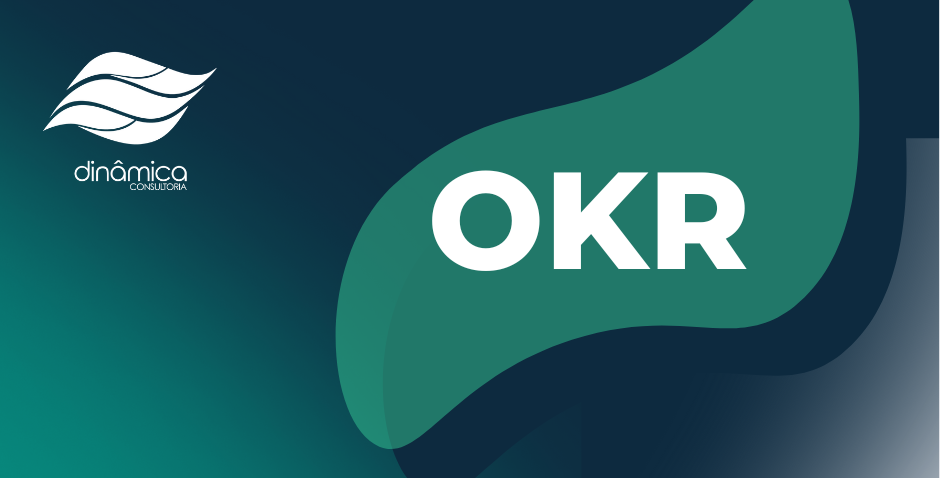
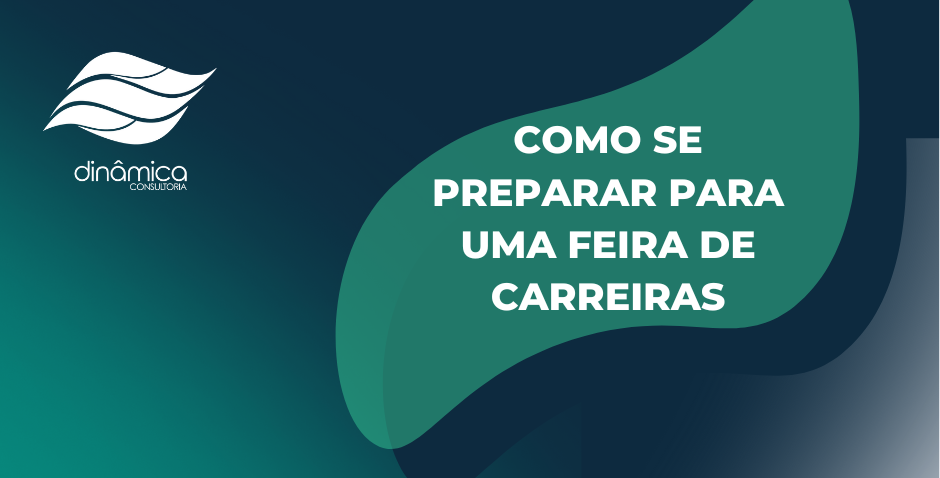
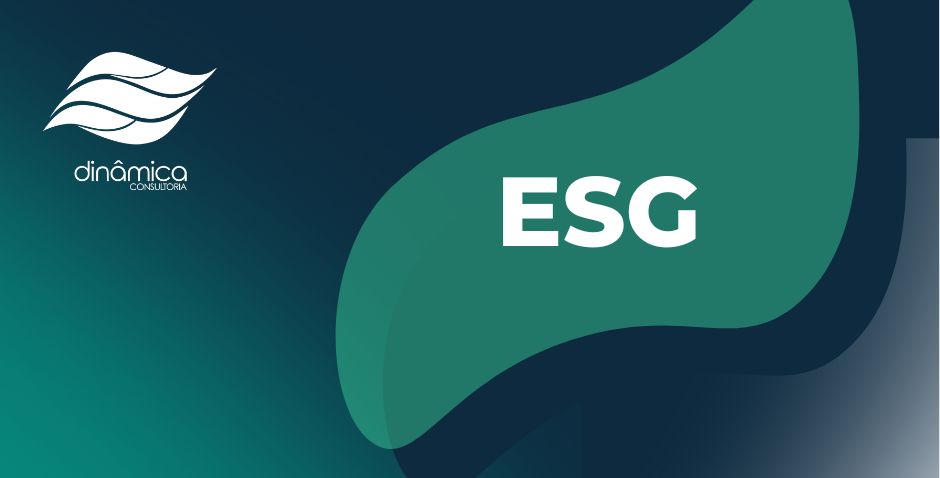
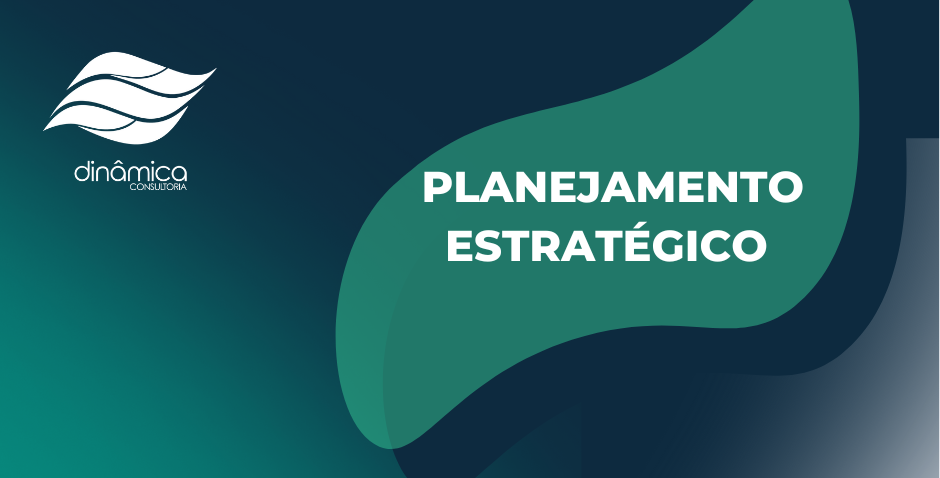
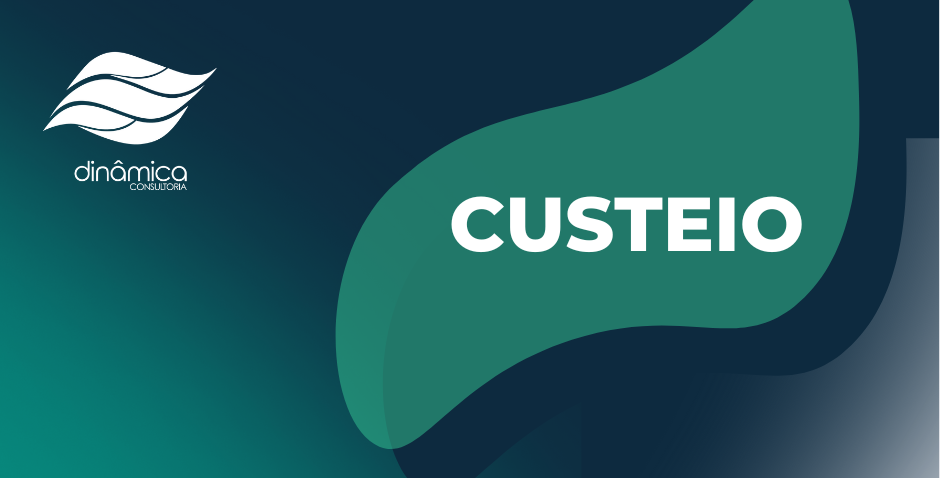